How Custom Metalwork Transforms Industrial Projects | 2025 Guide
Learn how custom metalwork supports industrial success. Explore its benefits, processes, trends, and why professional sheet metal fabrication services matter.
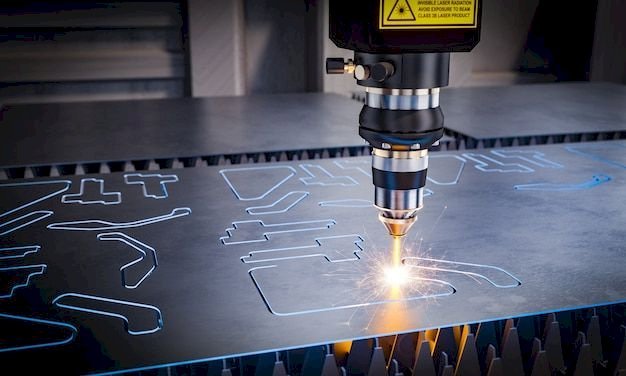
In today’s fast-paced industrial world, custom metalwork plays a crucial role in supporting innovation and progress across industries. Whether it is construction sites, factories, power plants, or transport systems, metal components are essential for creating strong structures, supporting heavy machinery, and building durable products. According to a recent report by Market Research Future, the global metal fabrication market is projected to reach USD 25 billion by 2030, driven by rising industrialisation and infrastructure development.
But what exactly is custom metalwork, and why is it so important for industrial projects? This article explores its meaning, benefits, types, processes, technological advancements, and real-world applications to show how it shapes industries across the UK and beyond.
What is Custom Metalwork?
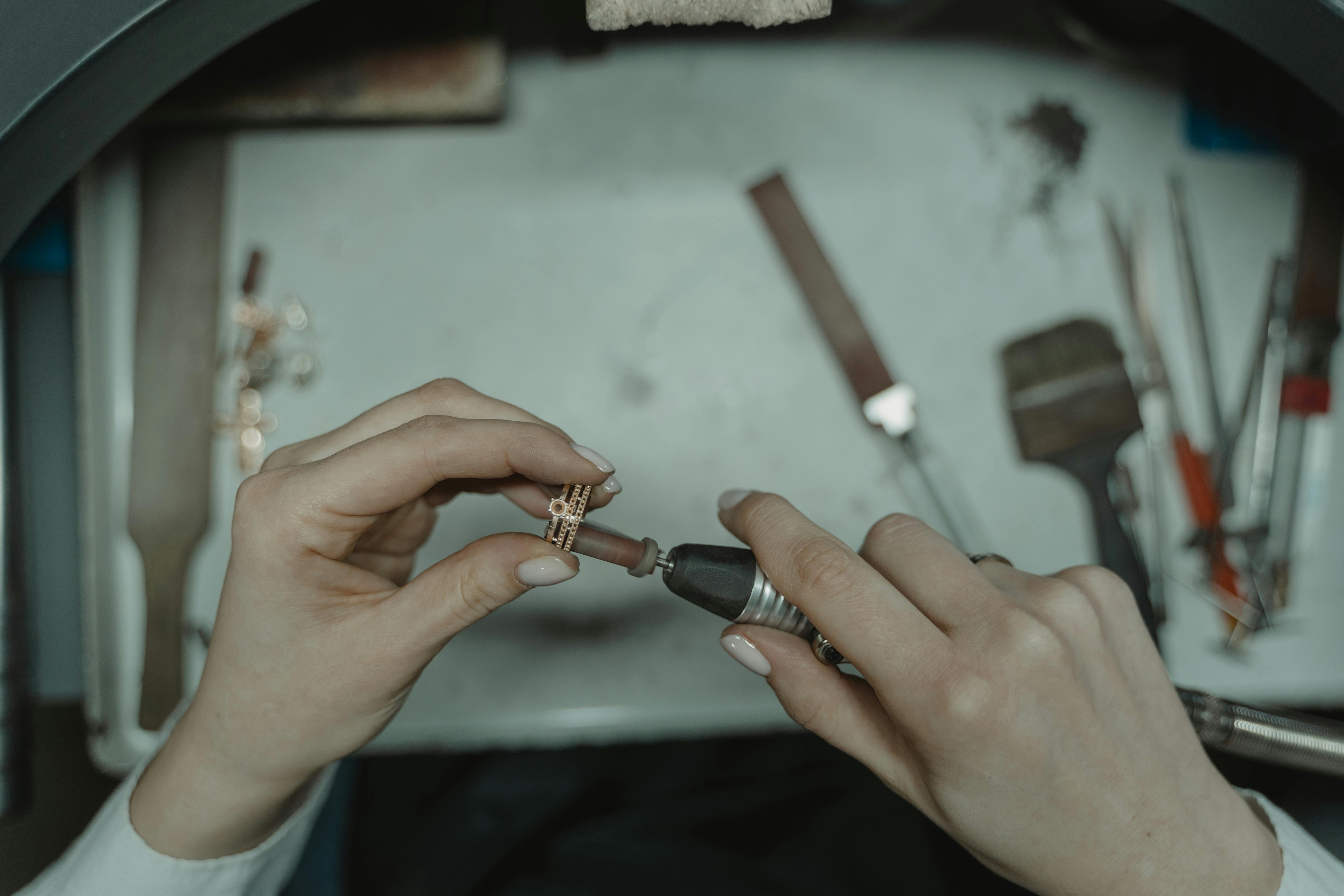
Image source: pexels.com
Custom metalwork involves designing, cutting, shaping, welding, and finishing metal parts tailored to specific project requirements. Unlike standard metal products, these components are crafted to meet exact measurements, functional needs, and design specifications.
Key Aspects of Custom Metalwork
-
Personalisation: Made for precise dimensions and uses
-
Material Choice: Stainless steel, aluminium, copper, brass based on need
-
Precision: Uses CNC machines, laser cutters, robotic welders for accuracy
-
Quality Control: Ensures parts meet standards and project requirements
Why is Custom Metalwork Important in Industrial Projects?

Image source: pixabay.com
1. Fits Unique Designs and Specifications
Modern industrial designs often go beyond standard sizes and shapes. Custom metalwork ensures each component fits its intended function and space, avoiding delays, rework, or structural risks.
2. Enhances Strength, Safety, and Durability
Industrial parts face high pressures, heat, and mechanical stress. Custom fabrication ensures the right thickness, alloys, and finishes are used for durability and safety.
3. Enables Complex Engineering
Industries today build advanced machinery and smart systems. Custom metalwork allows engineers and designers to bring these complex designs to life without being limited to standard parts.
4. Compliance with Industry Standards
Custom fabrication ensures parts meet UK regulations such as BS EN 1090 for structural steelwork, ISO standards, and sector-specific requirements, reducing safety and legal risks.
Common Types of Custom Metalwork Used in Industries

Image source: pixabay.com
Structural Metal Fabrication
Creates beams, columns, trusses, and frameworks essential for buildings, bridges, and industrial plants.
Sheet Metal Fabrication
Involves cutting, bending, and forming sheets into ducts, enclosures, panels, and housings used in HVAC systems, machinery covers, and construction. For these, companies rely on sheet metal fabrication services to ensure precision and compliance.
Pipe and Tube Fabrication
Creates pipelines, railings, and frameworks used in oil & gas, water treatment, and industrial settings.
CNC Machining
Computer-controlled cutting produces complex, precise parts for aerospace, automotive, and medical device industries.
Welding and Assembly
Joins different parts to create finished products like frames, platforms, and structural assemblies.
Laser Cutting and Waterjet Cutting
Allow intricate shapes with smooth edges for architectural panels or detailed machinery parts.
Read Also: Cosmetic Surgery Trends in 2025: What’s New, Popular, and Proven Safe
How Custom Metalwork Transforms Key Industrial Sectors
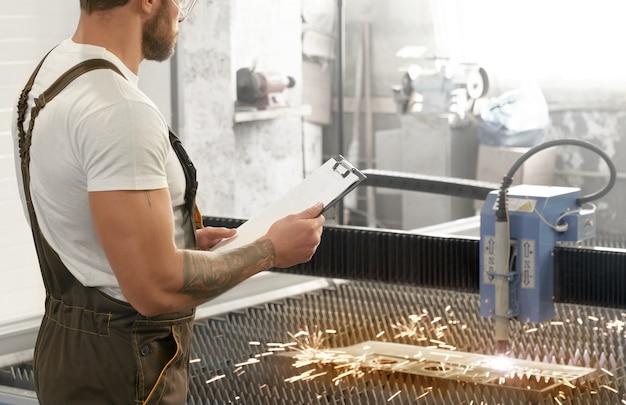
Image source: freepik.com
1. Construction
Steel beams, staircases, balcony railings, and façade frames are custom fabricated to meet design and load requirements. The UK construction sector uses over 1 million tonnes of structural steel annually, reflecting the demand for tailored solutions.
2. Manufacturing
Production lines, machine bases, conveyor systems, and storage racks are customised to optimise factory layouts and workflows.
3. Automotive
Custom chassis parts, brackets, and exhaust systems are created for specific vehicle models, supporting design accuracy and performance.
4. Energy and Utilities
Wind turbine towers, solar panel frames, and power plant structures require custom fabrication for strength and durability in outdoor conditions.
5. Food Processing and Pharmaceuticals
Stainless steel custom metalwork ensures hygiene and compliance with food-grade and cleanroom standards for workstations, tanks, and processing lines.
6. Aerospace and Defence
Precision metal parts support aircraft structures, landing gear, and military equipment where strength and accuracy are critical.
Benefits of Using Professional Custom Metalwork Services

Image source: pixabay.com
Advanced Technology Access
Professional fabricators use CNC laser cutters, robotic welders, and automated press brakes, achieving precise and efficient production.
Quality Assurance
Certified companies follow UK standards such as ISO 9001 and CE marking to ensure safety and reliability.
Time and Cost Savings
While custom parts may seem costly upfront, they reduce installation time, rework, and maintenance costs over their lifespan.
Design Expertise
Experienced fabricators provide design advice to improve strength, efficiency, and reduce material costs.
Scalability for Expansion
Designs can be replicated or modified easily to support future project expansions.
Key Processes in Custom Metalwork

Image source: freepik.com
1. Design and CAD Drafting
Creates detailed drawings, incorporating load calculations and tolerances to avoid errors during production and installation.
2. Material Selection
Metals are chosen based on strength, corrosion resistance, weight, and cost for each application.
3. Cutting
Laser cutting offers ±0.1 mm accuracy for thin sheets, while waterjet cutting handles thicker metals or heat-sensitive materials.
4. Forming and Bending
Press brakes bend metal sheets precisely; roll forming produces curved parts like pipes or cylinders.
5. Welding and Assembly
Robotic welding provides strong, consistent joints for structural safety.
6. Finishing
Processes like powder coating, galvanising, and polishing protect against corrosion and enhance appearance.
7. Quality Inspection
Final inspections include dimensional checks and non-destructive tests to ensure compliance and safety.
Read Also: Radiotherapy vs Chemotherapy: Understanding the Differences and Choosing the Right Treatment
Challenges in Custom Metalwork and How They Are Overcome
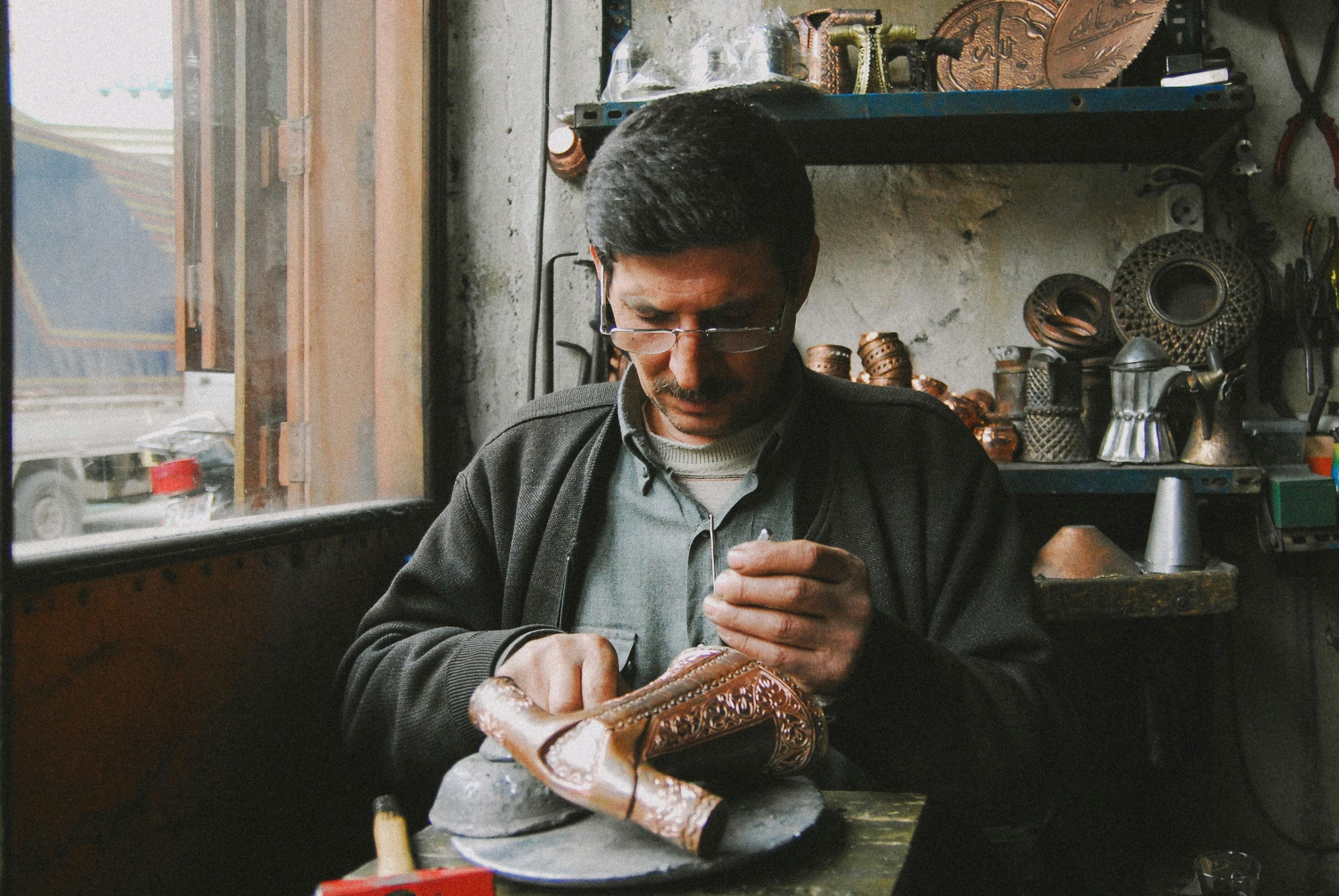
Image source: pexels.com
Managing Heavy Parts
Overhead cranes and forklifts handle large components safely during production.
Maintaining Precision
Advanced CNC machines and skilled technicians maintain tight tolerances required for safety-critical parts.
Reducing Waste
Nesting software optimises cutting layouts, reducing material waste and saving costs.
Skill Shortages
Companies invest in training, apprenticeships, and automation to address skilled labour gaps in the UK.
Innovations in Custom Metalwork (2025 Trends)
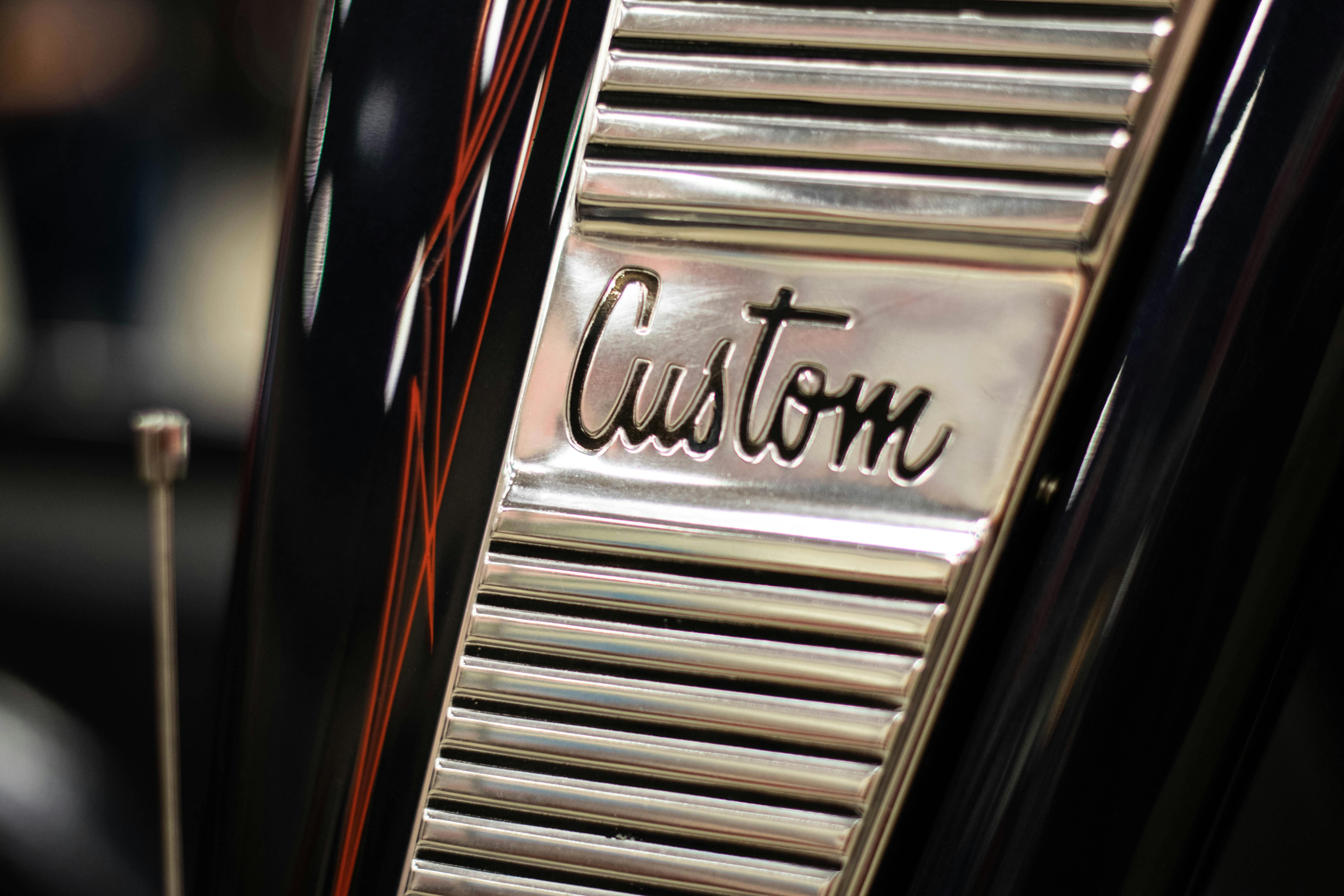
Image source: pexels.com
-
Robotic Welding: Increases productivity and weld consistency.
-
3D Metal Printing: Produces complex shapes without traditional cuts or welds, ideal for aerospace and medical sectors.
-
AI-Powered CAD Optimisation: Uses AI to design stronger, lighter, and cost-efficient parts.
-
IoT Integration: Monitors machine performance and predictive maintenance.
-
Sustainable Fabrication: Uses recycled metals and low-energy processes to support net-zero targets.
How to Choose the Right Custom Metalwork Service Provider
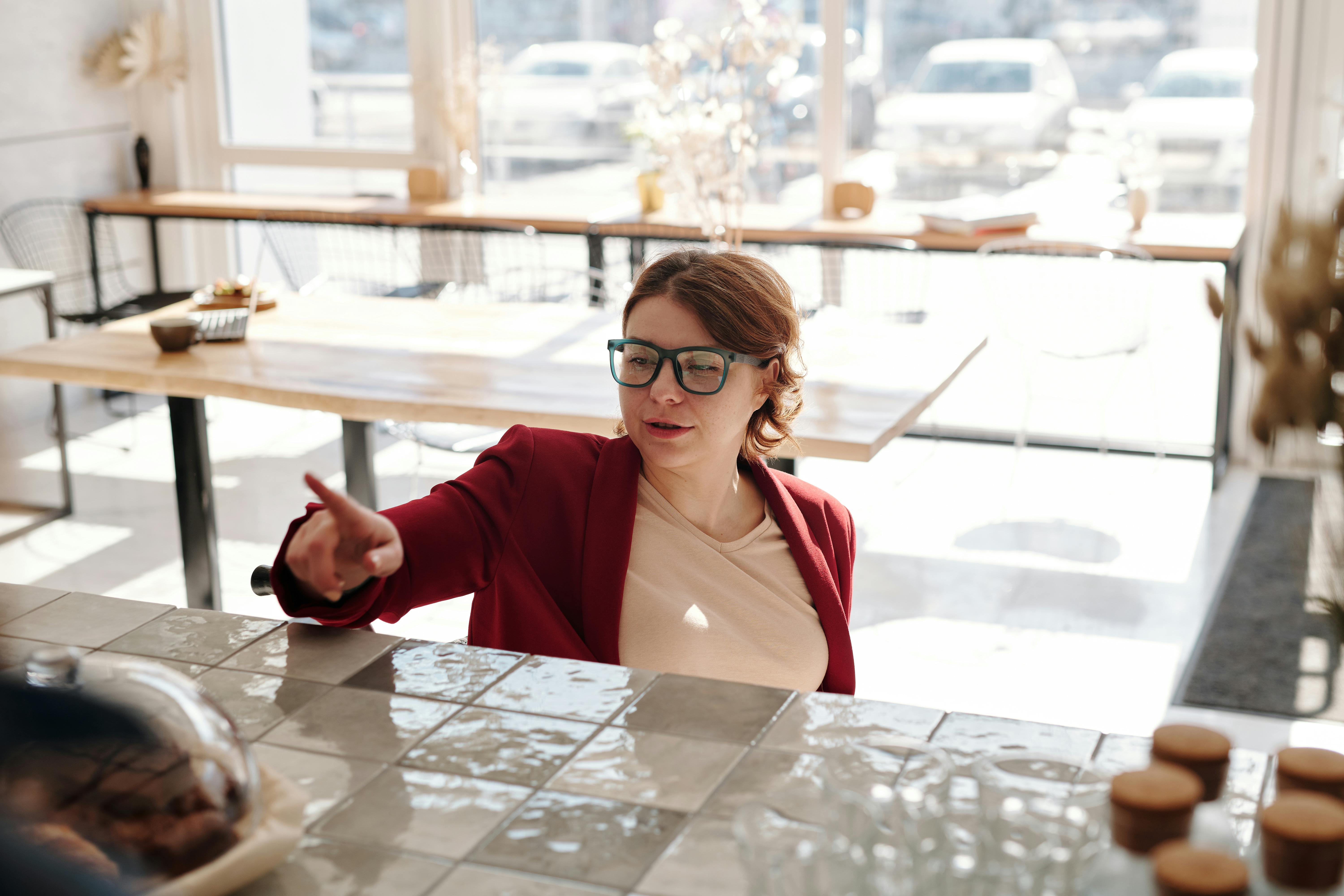
Image source: pexels.com
-
Assess Technical Capabilities – Ensure they handle your project’s size and complexity.
-
Check Certifications – Look for ISO, CE, and industry-specific standards.
-
Review Past Projects – Experience in similar sectors shows expertise.
-
Evaluate Design Support – Providers offering design refinement add value.
-
Discuss Delivery and Logistics – Check installation services and transport options.
-
Get Clear Quotations – Detailed quotes prevent budget surprises.
Real-Life Example: Renewable Energy Project

Image source: pexels.com
A UK renewable energy firm building offshore wind farms partnered with a fabricator to produce custom turbine tower sections and platforms. Standard parts couldn’t handle marine conditions. The company:
-
Used marine-grade steel with anti-corrosion coatings
-
Conducted structural analysis for strength
-
Delivered parts modularly for easy on-site assembly
This approach cut maintenance costs by 25% and improved operational efficiency, supporting their green energy goals.
Conclusion
Custom metalwork is essential for industrial projects that require precise, durable, and tailored solutions. Whether creating factory machinery frames, building structures, or energy system parts, custom fabrication ensures safety, efficiency, and compliance with regulations. As technologies like robotic welding, AI-driven design, and 3D metal printing continue to evolve, custom metalwork will become even more accurate, cost-effective, and sustainable. Partnering with experienced professionals for your sheet metal fabrication services and custom metalwork needs ensures reliable results and long-term success for any project.
FAQs
Q1. What metals are used in custom metalwork?
A1. Stainless steel, aluminium, mild steel, copper, and brass are commonly used based on project needs.
Q2. Is custom metalwork expensive?
A2. While initial costs are higher than standard parts, long-term savings come from durability, perfect fit, and reduced rework.
Q3. How long does fabrication take?
A3. From design to delivery, it can range from a few days to weeks, depending on complexity.
Q4. How does 3D metal printing help?
A4. It produces complex parts quickly, reduces waste, and enables rapid prototyping.
Q5. What industries use custom metalwork most?
A5. Construction, manufacturing, automotive, aerospace, energy, food processing, and pharmaceuticals.